Optical bonding is used to laminate touch screens or cover glass to display. Special glue and a unique manufacturer’s technology are required for the entire operation. Optical bonding technology also allows connecting a display with transparent layers of electromagnetic protection or with special coatings, e.g. AG (anti–glare), AR (anti–reflective), HC (hard coating) and polarizing filters.
The advantages of optical bonding:
Reduced reflections and refractions-in air bonding, light from an external source passes through the panel and air gap (between the display and the glass), causing its refraction. This phenomenon means that some of the light is reflected back, creating reflections on the screen. light generated by the backlight of the LCD module, goes through the boundaries of materials with different refractive index (4%), which causes partial deflection. The results are reduced contrast and legibility of the display. The adhesive used in optical bonding reduces the refraction effect, as the refractive index of the adhesive is similar to glass.
Increase the brightness-By bonding the LCD module and glass together it removes the interruptions and chances for the light to be reflected back. More light gets through to the surface of the screen and therefore the image is brighter.

Prevents from dust and condensation-The most obvious benefit to adding a resin bonding layer between the glass and LCD module is that it physically prevents dust and liquid ingress from getting between the two. The dust and water isn’t a big problem for screens in standard environments. What can be a problem however is condensation getting between the glass and LCD panel in environments with wide temperature ranges or fluctuating humidity. Condensation can cause screens to become foggy from moisture that penetrates the air gap. Again, the physical filling of the gap prevents this problem from arising. Optical bonding should therefore be considered for any outdoor application as well as indoor applications e.g. production halls and warehouses, in hospitals.



The advantage of silicone optical bonding
Control curing process-It use UV light to cure acrylics, the processing happens very fast, the areas wont cure if didn’t get illuminated, so there may have uncured acrylics remaining underneath of the black mask printing, on the opposite, the silicones cure as soon as two components got mixed, the reaction is relatively slow. It can accelerate the temperature during the process, enable the silicones cure evenly

Very low curing shrinkage-all adhesive experience some shrinkage during cure, the shrinkage rate of silicone is below 0.1% whereas acrylic shrinkage is about 4%, the higher shrinkage cause the mechanical forces on the display which can cause bright spots as well as discolorations
Hardness adjustable-Some products may require a different material hardness than others, the hardness of acrylics is predefined which impossible to change, but silicones is a simple silicones a simple variation of the mixing ratio can change the materials hardness in a wide range

Low yellowing fill material and huge temperature range-acrylic material require an operating temperature range of only -30 to +80°C and medium-term yellowing while silicone, which the silicone with features an operating temperature range of -40 to + 120°C and shows minor yellowing


See the difference between optical bonding and air bonding:
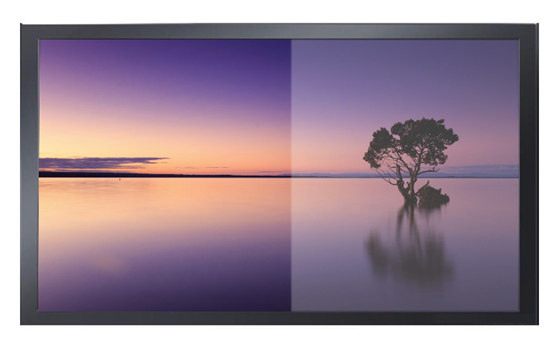